Semiconductor
Pressure instruments for semiconductor manufacturing
The global semiconductor industry’s significant growth in recent years is expected to continue through 2021 and beyond. Key contributing factors include the increase in the incorporation of microelectronics in electrical and electronic devices, artificial intelligence, IoT (Internet of Things), and the expansion of Industry 4.0 initiatives. As these changes occur, semiconductor suppliers face the challenge of improving supply to meet demand—i.e., increasing transistor density, improving reliability, and, of course, reducing production and purchasing costs.
Ashcroft is ready and willing to help semiconductor manufacturers take on and overcome this challenge. Equipped with extensive industry-specific experience, we have the knowledge and skills to help develop, engineer, manufacture, and test the instruments and equipment necessary for high-quality semiconductor production.
We offer a variety of pressure measurement products—including transmitters with our proprietary ultra-stable CVD sensing technology—suitable for use in semiconductor manufacturing applications. The performance of our products are coupled with global safety approvals and a legacy of performance in the most critical semiconductor applications.
In semiconductor tools, the gas panel controls the flow of gas into the process chamber. Pressure transducers are installed inside of the gas panel on each of the gas sticks to monitor the pressure output of the pressure regulator. This position enables them to send signals that adjust system operation with greater precision, accuracy, and speed, resulting in better overall system function.
Some of the gases used in semiconductor applications are toxic, flammable, and otherwise dangerous to those handling them. These dangers necessitate ATEX and IECEx hazardous location approval for many products. Ashcroft and Nagano Keiki Co. Ltd. of Japan (our parent company) annually produce over 100,000 pressure transmitters and gauges designed and engineered for safe use in semiconductor industry applications.
Hydrogen is one of the most common carrier gases used in UHP gas delivery. Safely handling hydrogen requires the implementation of protective measures that mitigate the risk of fire or explosion. Preferred methods include Intrinsic Safety and Non-Sparking Approvals. One critical factor to keep in mind is the effect of hydrogen embrittlement. The stability and repeatability of pressure transmitters and gauges rely on their measuring mechanisms (directly tied to the metallurgy and their resistance to embrittlement). Ashcroft high-purity transmitters and gauges utilize high-purity austenitic 316L stainless steel, which has been shown to mitigate the effects of hydrogen embrittlement.
The amount of pressure needed to prevent contaminants from infiltrating cleanrooms and other clean spaces is highly specific. Too little pressure results in unwanted particles entering the area, while too much pressure causes excessive air movement and wasted energy. Pressure transducers and gauges integrated into the air handling equipment must be extremely sensitive, accurate, and reliable.
The semiconductor manufacturing process involves the highly complex transformation of a blank silicon wafer into discrete microelectronic devices. A circuit design and pattern are developed, which are then etched onto the wafer. The wafers can then be broken into individual circuits to be used in electronic devices. Semiconductor manufacturing is continually challenged to increase the amount and density of the circuitry that can fit into each wafer. Wet etching uses aggressive chemicals to perform microfabrication.
The process of dry etching, including Reactive Ion Etching (RIE), is commonly used to form contact holes on silicon wafer patterns. It uses reactive gases such as fluorocarbons, oxygen, chlorine and boron trichloride. Ashing is a similar process as dry etching to remove the photoresist (light-sensitive coating) on the wafer. Plasma ashing uses oxygen or fluorine gases, and it is important to control the flow rate of these gases that require accurate pressure measurement.
The process of Chemical Vapor Deposition (CVD) in the semiconductor industry involves using a carrier gas, such as Nitrogen or Oxygen, to dilute a toxic gas, such as Phosphine or Nitrous Oxide. Semiconductor gases can be flammable, toxic and explosive, so careful selection of a pressure transducer with appropriate approvals for intrinsic safety or non-incendive locations must be made to address critical safety concerns.
Ultrapure water is treated to the highest levels of purity for all contaminant types, and deionized water has all organic particles and dissolved gases removed. Semiconductor processes such as wafer cleaning require ultrapure and deionized water to prevent contamination in the application from foreign particles creating defects and damage to the exposed wafer surfaces.
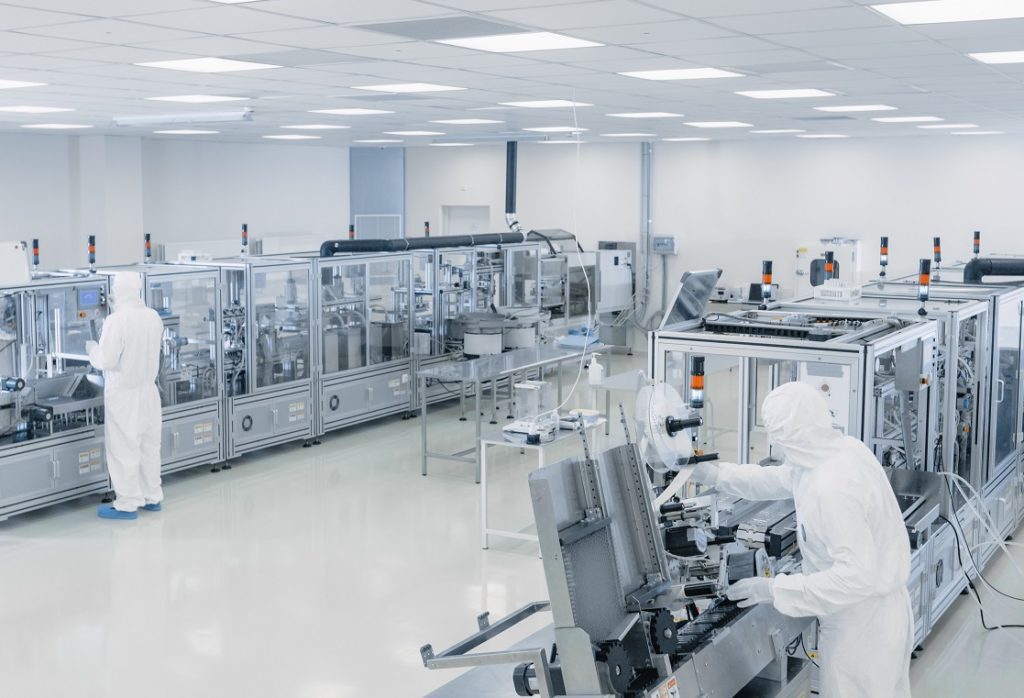
Importance of Pressure Measurement in Semiconductor Manufacturing
Today, semiconductor manufacturing operations rely on the precise and accurate delivery of ultra-high purity (UHP) gases, which require purity levels to exceed 99.9995% and stringent control over stray particles and moisture. Given the importance of UHP gas supply systems, the measurement and control technologies utilized for their distribution must offer high-precision, high-accuracy performance while maintaining absolute cleanliness inside the system. Construction materials must remain inert when in contact with the UHP gases, minimize the risk of trapped (dead) volume, and prevent particle shedding and entrapment.
While essential to the manufacture of modern semiconductors, the toxicity and flammability of UHP gases pose significant risks to the health and well-being of those handling them. For this reason, some devices used in semiconductor operations are required to comply with leak integrity and hazardous location specifications and standards (e.g., ATEX and IECEx) to assure user safety.
Ashcroft Pressure Instruments for Semiconductor Manufacturing
ZT High-Purity Transmitters and HPX High Purity Pressure Gauges
Our ZT/ZX pressure transmitters and HPX pressure gauges are specially designed for use in semiconductor applications. These products feature electropolished 316L stainless steel wetted parts and VCR-compatible, modular and weld tube fittings with minimal dead volumes. They have compact designs that accommodate higher density mounting configurations inside gas boxes and gas delivery systems. The ZX11 includes ATEC and IECEx hazardous location approvals.
ZL91 Pressure Transducer, ZL92 Pressure Transducer and HPT - 63 mm Pressure Gauge
The Ashcroft ZL91 pressure transducer is constructed with fluoropolymer (PTFE/PFA) wetted parts that minimize metal ion elution. Its compact design helps to reduce contamination and maintain the purity of your process fluid. This transducer is well suited for ultrapure/de-ionized water facilities and equipment, cleaning equipment for semiconductor and wet station applications.
The Ashcroft ZL92 pressure transducer is designed for use in semiconductor processes that require PTFE/PFA wetted parts for improved chemical compatibility for use in corrosive gases and fluids, including Hydrofluoric acid or other aggressive acids. A secondary isolation diaphragm and vent design isolate the ceramic sensing element from corrosive gases and liquids, which extends the life span of the transducer. This transducer works well in cleaning equipment for semiconductor, wet etching and chemical supply systems.
The Ashcroft 63 mm HPT anti-corrosion pressure gauge offers exceptional performance and reliability for chemical delivery systems within the semiconductor and electronic fabrication industries. It’s nitrogen leak tested to ensure superior integrity, while the compact design is ideal for limited space installations. The gauge is made with fluoropolymer wetted parts making it compatible with processes that use corrosive or non-contaminating fluids. In non-contaminating processes, the wetted parts prevent metal ion elution – perfect for ultrapure or deionized water processes.
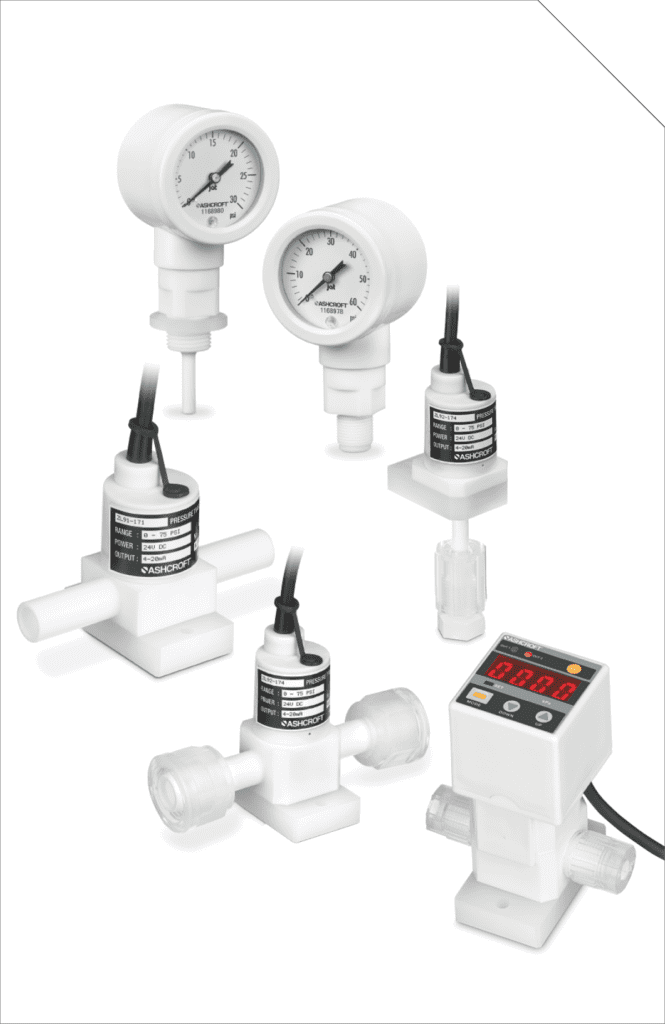
Low Differential Pressure Transmitters and Transducers for Clean Rooms and Clean Spaces
Many of our differential pressure transducers—including DXLdp, CXLdp, AXLdp, and GC30— are integrated with Si-GlasⓇ technology, which helps them accommodate the highly critical monitoring and control needs of ultra-low differential pressure applications. Pressure ranges as low as 0.05 in H2O (12.5 Pa) allow for the tightest control at incredibly low pressures.
Our 1130 Series gauges are designed for incorporation into glove boxes, wafer handling equipment, and wall panels with differential pressure ranges as low as 0.6 in H2O (150 Pa).
FAQs
Are there other scales and dial options for the HPX pressure gauges?
Yes, other pressure units, ranges or custom dials can be accommodated upon request but may be subject to minimum quantities.
Are there other pressure connections available on the ZT/ZX pressure transmitters?
Other pressure fittings (such as weld/tube stub or VCO) can be accommodated upon request but may be subject to minimum quantities.
How are the Ashcroft high purity products packaged?
All ZT/ZX and HPX high purity instruments are packaged in two (2) Plastic (PE) bags purged with Nitrogen.
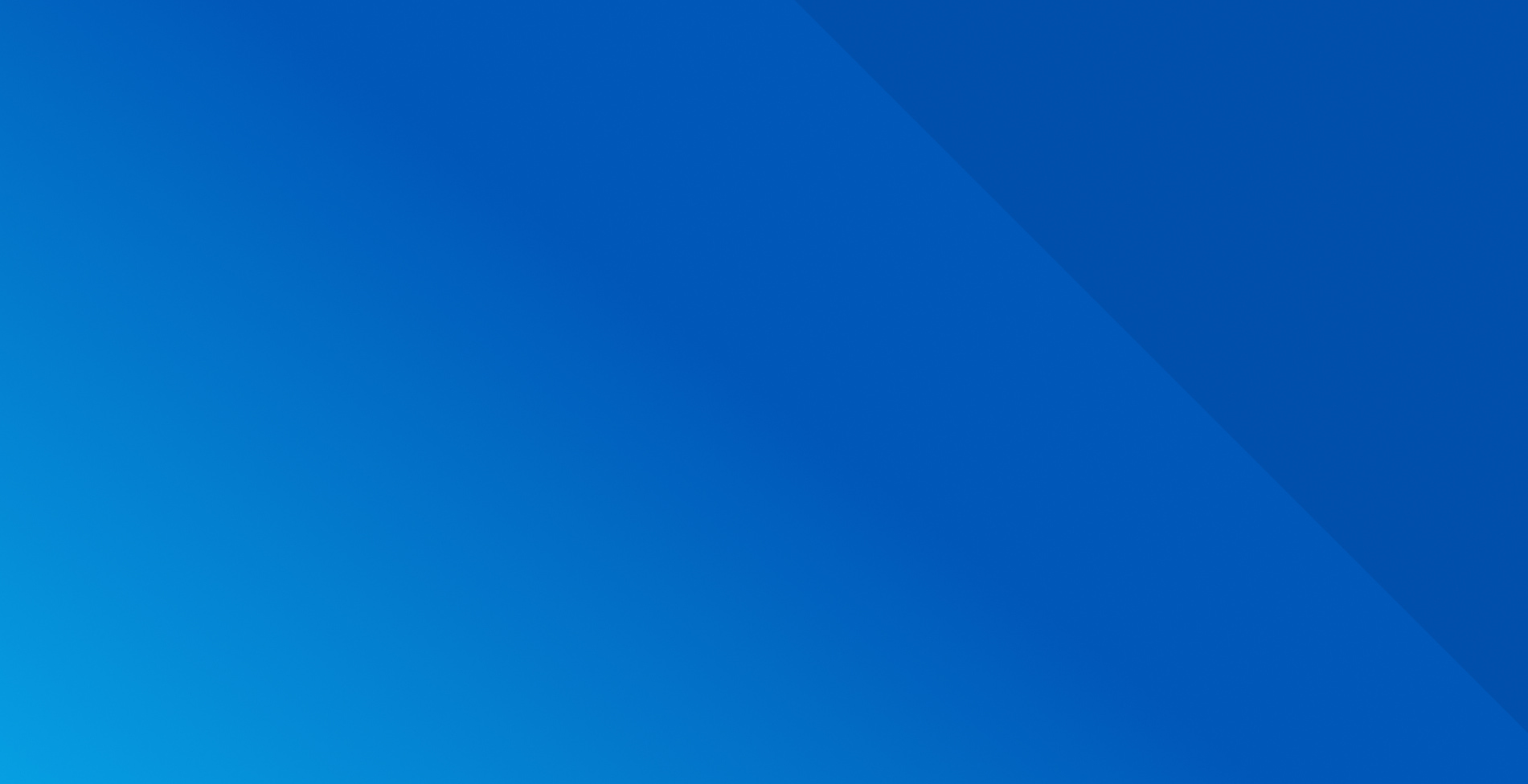
Trust In the Ashcroft Experts
At Ashcroft, we are here to help you identify the right pressure and temperature instrumentation. We have designed pressure measuring instruments for Ultrapure and Deionized Water Etching, Gas Panel and Gas Delivery Systems for semiconductor applications.